AT-Closed Vial® and Container Closure Integrity during Cryogenic Storage
More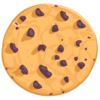
We use cookies to offer you the best experience on our site. You can find out more about the cookies we use or disable them in the Cookie settings
The use of an isolator for biopharma manufacturing keeps on trending, since it implies lower installation requirements and strong reduction of contamination, by creating a controlled environment and decontamination of the material, operating chambers and equipment.
Result of collaboration between Aseptic Technologies, SKAN and our users, the pure M1 is the first isolated fill & finish unit, dedicated to small cGMP batches.
The pure M1 combines the AT-Closed Vial® technology and the isolator shell by SKAN pure Solutions. It consists in an isolator with integrated manual filling equipment, rapid material airlock and an exit laminar airflow.
The overall design was performed in tight cooperation with end-users, resulting in deep understanding of the processes involved and providing an ergonomic solution.
The pure M1 contains the semi-automated AT-Closed Vial® filling process within the pure isolator by SKAN.
The ready-to-use material (AT-Closed Vial® in AT-CryoBox, AT-Cap in rigid support bases, fluid path AT-Filling Kit) is introduced through a rapid decontamination airlock, the bulk product is passed directly to the main chamber through aseptic liquid connector, the AT-Port System, to keep the bulk outside of the isolator, where it can be cooled and homogenized.
In the main chamber, the AT-Closed Vial® are semi-automatically filled, laser re-sealed and capped with a snap fit. The dosing system, a peristaltic pump, provides high accuracy and is easily calibrated thanks to an integrated weighting cell.
Overall batch status is demonstrated live on the built-in screen in the back of the isolator chamber. The filled vials in AT-CryoBox can be continuously brought outside of the isolator through a mousehole and an exit laminar airflow on the right.
Standard decontamination cycle for a maximal load, validated cleaning procedures and the full Validation Master Plan for the AT-Closed Vial® technology are provided.
AT-Closed Vial® and Container Closure Integrity during Cryogenic Storage
More