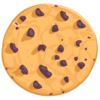
We use cookies to offer you the best experience on our site. You can find out more about the cookies we use or disable them in the Cookie settings
Single-use devices are deeply enrooted in the life science, pharmaceutical, diagnostic and medical industries. The use of plastics for prototyping and serial manufacturing for these applications is particularly important and can’t be limited, due to the high purity, precision and functionality requirements.
Such narrow tolerances and cleanliness can be achieved with precision injection molding in adequate clean environment.
Besides, to maintain the cleanliness chain, the devices are often required to be ready-to-use, meaning that they are fully prepared, adequately packed and sterilized.
It’s in our DNA: design, injection molding and radiation sterilization of pharmaceutical devices.
Since its creation, Aseptic Technologies has developed a unique expertise in design and highly controlled validated clean manufacturing process of :
We master the core requirements for pharmaceutical devices since 2002, including the most critical product contact parts. And we will leverage this expertise for your project.
Founded in 2021 as a joint project of Aseptic Technologies, Simonis Plastic and SRIW Group, Plast4Life provides clean custom injection molding services to life science companies.